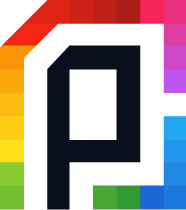
Health and safety engineers develop procedures and design systems to keep people from getting sick or injured and to keep property from being damaged. They combine a knowledge of health or safety and of systems engineering to make sure that chemicals, machinery, software, furniture, and other products are not going to cause harm to people or buildings.
Health and safety engineers typically do the following:
Health and safety engineers also investigate industrial accidents, injuries, or occupational diseases to determine their causes and to see whether they could have been or can be prevented. They interview employers and employees to learn about work environments and incidents leading up to accidents or injuries. They also evaluate the corrections that were made to remedy violations found during health inspections.
Health and safety engineers are also active in two related fields: industrial hygiene and occupational hygiene.
In industrial hygiene, they focus on the effects of chemical, physical, and biological agents. They recognize, evaluate, and control these agents to keep people from getting sick or injured. For example, they might anticipate that a particular manufacturing process will give off a potentially harmful chemical and recommend either a change to the process or a way to contain and control the chemical.
In occupational hygiene, health and safety engineers investigate the environment in which people work and use science and engineering to recommend changes to keep workers from being exposed to sickness or injuries. They help employers and employees understand the risks and improve working conditions and working practices. For example, they might observe that the noise level in a factory is likely to cause short-term and long-term harm to workers and recommend ways to reduce the noise level through changes to the building or by having workers wear strong headphones.
Health and safety engineering is a broad field covering many activities. The following are specific types of health and safety engineers:
Aerospace safety engineers work on missiles, radars, and satellites to make sure that they function safely as designed.
Fire prevention and protection engineers design fire prevention systems for all kinds of buildings. They often work for architects during the design phase of new buildings or renovations. They must be licensed, and they must keep up with changes in fire codes and regulations.
Product safety engineers investigate the causes of accidents or injuries that might have resulted from the use or misuse of a product. They propose solutions to reduce or eliminate any safety issues associated with products. They also participate in the design phase of new products to prevent injuries, illnesses, or property damage that could occur with the use of the product.
Systems safety engineers work in many fields, including aerospace, and are moving into new fields, such as software safety, medical safety, and environmental safety. These engineers take a systemic approach to identify hazards in these new fields so that accidents and injuries can be avoided.
For information on health and safety engineers who work in mines, see the profile on mining and geological engineers.
Occupational health and safety technicians collect data on the safety and health conditions of the workplace. Technicians work with occupational health and safety specialists in conducting tests and measuring hazards to help prevent harm to workers, property, the environment, and the general public. For more information, see the profile on occupational health and safety specialists.
Occupational health and safety technicians typically do the following:
Technicians conduct tests and collect samples and measurements as part of workplace inspections. For example, they may collect and handle samples of dust, mold, gases, vapors, or other potentially hazardous materials. They conduct both routine inspections and special inspections that a specialist orders. For more information about specialists, see the profile on occupational health and safety specialists.
Technicians may examine and test machinery and equipment such as scaffolding and lifting devices to be sure that they meet appropriate safety regulations. They may check that workers are using protective gear, such as masks and hardhats, as regulations say they must.
Technicians also check that hazardous materials are stored correctly. They test and identify work areas for potential health and safety hazards.
In addition to making workers safer, technicians work with specialists to increase worker productivity by reducing the number of worker absences and equipment downtime. They save companies money by lowering insurance premiums and worker compensation payments and by preventing government fines.
Technicians' duties vary based on where they are employed. For example, a technician may test the levels of biohazard at a waste processing plant or may inspect the lighting and ventilation in an office setting. Both of these inspections are focused on maintaining the health of the workers and the environment.
The responsibilities of occupational health and safety technicians vary by industry, workplace, and types of hazards affecting employees. The following are examples of types of occupational health and safety technicians:
Environmental protection technicians evaluate and coordinate the storage and handling of hazardous waste, the cleanup of contaminated soil or water, evaluation of air pollution, or other activities that affect the environment.
Health physics technicians work in places that use radiation and radioactive material. Their goal is to protect people and the environment from hazardous radiation exposure.
Industrial hygiene technicians examine the workplace for health hazards, such as exposure to lead, asbestos, pesticides, or contagious diseases.
Mine examiners inspect mines for proper air flow and health hazards such as the buildup of methane or other harmful gases.
Construction and building inspectors ensure that new construction, changes, or repairs comply with local and national building codes and ordinances, zoning regulations, and contract specifications.
Construction and building inspectors typically do the following:
Construction and building inspectors examine buildings, highways and streets, sewer and water systems, dams, bridges, and other structures. They also inspect electrical; heating, ventilation, air-conditioning, and refrigeration (HVACR); and plumbing systems. Although no two inspections are alike, inspectors do an initial check during the first phase of construction and follow-up inspections throughout the construction project. When the project is finished, they do a final, comprehensive inspection.
The following are types of construction and building inspectors:
Building inspectors check the structural quality and general safety of buildings. Some specialize in structural steel or reinforced-concrete structures, for example.
Electrical inspectors examine the installed electrical systems to ensure they function properly and comply with electrical codes and standards. The inspectors visit worksites to inspect new and existing sound and security systems, wiring, lighting, motors, and generating equipment. They also inspect the installed electrical wiring for HVACR systems and appliances.
Elevator inspectors examine lifting and conveying devices, such as elevators, escalators, moving sidewalks, lifts and hoists, inclined railways, ski lifts, and amusement rides.
Home inspectors typically inspect newly built or previously owned homes, condominiums, townhomes, and other dwellings. Prospective home buyers often hire home inspectors to check and report on a home's structure and overall condition. Sometimes, homeowners hire a home inspector to evaluate their home's condition before placing it on the market.
In addition to examining structural quality, home inspectors examine all home systems and features, including roofing, exterior walls, attached garage or carport, foundation, interior, plumbing, electrical, and HVACR systems. They look for and report violations of building codes, but they do not have the power to enforce compliance with the codes.
Mechanical inspectors examine the installation of HVACR systems and equipment to ensure that they are installed and function properly. They also may inspect commercial kitchen equipment, gas-fired appliances, and boilers.
Plan examiners determine whether the plans for a building or other structure comply with building codes. They also determine whether the structure is suited to the engineering and environmental demands of the building site.
Plumbing inspectors examine the installation of potable water, waste, and vent piping systems to ensure the safety and health of the drinking water system, piping for industrial uses, and the sanitary disposal of waste.
Public works inspectors ensure that federal, state, and local government water and sewer systems, highways, streets, bridges, and dam construction conform to detailed contract specifications. Workers inspect excavation and fill operations, the placement of forms for concrete, concrete mixing and pouring, asphalt paving, and grading operations. Public works inspectors may specialize in highways, structural steel, reinforced concrete, or ditches. Others specialize in dredging operations required for bridges and dams or for harbors.
Specification inspectors ensure that work is performed according to design specifications. Specification inspectors represent the owner's interests, not those of the general public. Insurance companies and financial institutions also may use their services.
A primary concern of building inspectors is fire prevention safety. For more information, see the profile on fire inspectors and investigators.
Sales managers direct organizations' sales teams. They set sales goals, analyze data, and develop training programs for the organization's sales representatives.
Sales managers typically do the following:
Sales managers' responsibilities vary with the size of the organization they work for. However, most sales managers direct the distribution of goods and services by assigning sales territories, setting sales goals, and establishing training programs for the organization's sales representatives.
In some cases, they recruit, hire, and train new members of the sales staff. For more information about sales workers, see the profiles on retail sales workers and wholesale and manufacturing sales representatives.
Sales managers advise sales representatives on ways to improve their sales performance. In large multiproduct organizations, they oversee regional and local sales managers and their staffs.
Sales managers also stay in contact with dealers and distributors. They analyze sales statistics that their staff gathers, both to determine the sales potential and inventory requirements of products and stores and to monitor customers' preferences.
Sales managers work closely with managers from other departments. For example, the marketing department identifies new customers that the sales department can target. The relationship between these two departments is critical to helping an organization expand its client base. Because sales managers monitor customers' preferences and stores' and organizations' inventory needs, they work closely with research and design departments and warehousing departments.
Structural iron and steel workers install iron or steel beams, girders, and columns to form buildings, bridges, and other structures. They are often referred to as ironworkers.
Ironworkers typically do the following:
Iron and steel are important parts of buildings, bridges, and other structures. Even though the primary metal involved in this work is steel, these workers often are known as ironworkers or erectors.
When building tall structures such as a skyscraper, ironworkers erect steel frames and assemble the cranes and derricks that move structural steel, reinforcing bars, buckets of concrete, lumber, and other materials and equipment around the construction site. Once this job has been completed, workers begin to connect steel columns, beams, and girders according to blueprints and instructions from construction supervisors.
As they work, they use a variety of tools. They use rope (called a tag line) to guide the steel while it is being lifted; they use spud wrenches (long wrenches with a pointed handle) to put the steel in place; and they use driftpins or the handle of the spud wrench to line up the holes in the steel with the holes in the framework. To check the alignment, they may use plumb bobs, laser equipment, or levels.
Structural steel generally comes to the construction site ready to be put up--cut to the proper size, with holes drilled for bolts and numbered for assembly.
Some ironworkers make structural metal in fabricating shops, which are usually located away from the construction site. For more information, see the profile on assemblers and fabricators.